CARTA - CARTONE -
CELLOFAN - VETRO
La carta è un foglio di
natura igroscopica, composto essenzialmente di materie prime fibrose
vegetali, opportunamente essiccate; ha uno spessore che varia da 0,02 a 0,3
mm. e una grammatura (peso per metro quadrato, espresso in grammi) che varia
da 10 ad oltre 300 g/m2.
La prima macchina per la
fabbricazione della carta fu realizzata in Francia da Luigi Robert alla fine
del XVIII: il foglio che ne usciva aveva una larghezza di circa 60
centimetri. Appena pochi anni dopo, nel 1804, in Inghilterra fu realizzata
una macchina con luce di 152 centimetri. Oggi, le moderne macchine per la
fabbricazione della carta, raggiungono un’altezza di sei metri (in Italia 3-4
metri) e il foglio finito esce ad una velocità che può raggiungere i 400
metri al minuto. I progressi, quindi, sono stati enormi e proporzionali
all’importanza sempre maggiore che la carta ha ottenuto, anche nel campo
dell’imballaggio, nel corso di questi ultimi anni. Ormai, praticamente, si
può dire che quasi tutto può essere confezionato o imballato in carta e
cartone; persino i prodotti liquidi (latte, vino, ecc,) possono essere
condizionati in carta opportunamente trattata. Si tratta, pertanto, di un
materiale della massima importanza nell’industria dell’imballaggio e la sua
trattazione in poche pagine richiede una notevole sintesi degli argomenti da
esporre; cercheremo quindi di descrivere, nel modo il più possibile chiaro e conciso, le
caratteristiche essenziali di questo materiale che, da solo costituisce circa
il 50% degli imballaggi tuttora realizzati in Italia. Le materie prime per la
fabbricazione della carta si possono dividere in quattro categorie.
La prima categoria è costituita dalle
materie fibrose vegetali. Stracci di cotone, canapa, juta, lino, pur se molto
usati per altri tipi di carta, vengono raramente impiegati per la carta
destinata all’imballaggio.
Per essa si utilizzano cellulose
chimiche di conifere, di paglia e di altri vegetali, pasta legno di abete e
di pioppo, e, per le carte di minimo pregio, ritagli di carta da giornale,
cartaccia e scatole o ritagli di cartone usati.
Nella preparazione di cellulose
chimiche, si opera in maniera tale da portare in soluzione tutte le sostanze
estranee alla cellulosa, La cellulosa che rimane libera dopo il procedimento
ha un peso parti al 50% del peso del legno da cui si è partiti. Per ottenere
tale suddivisione si seguono due procedimenti: il procedimento alcalino al
solfato – impiegato per la fabbricazione di cellulosa Kraft, destinata alla
realizzazione di cartone ondulato e di sacchi a più pareti – e il
procedimento acido al bisolfito di calcio.
La pasta legno si ottiene invece
sfibrando dei tondelli di legno contro delle pietre rotanti.
Nell’imballaggio si usa anche la pasta
semichimica, che si ottiene mediante un particolare trattamento con opportuni
reagenti.
La seconda categoria di materie prime
per la carta è costituita dalle sostanze di carica. Tali sostanze (caolino e
gesso, in massima parte) vengono aggiunte all’impasto per migliorare le
caratteristiche della carta, per eliminare le porosità e per aumentarne il
peso.
La terza categoria è costituita dalle
sostanze collanti. Queste sostanze non vengono però di regola aggiunte
all’impasto nella fabbricazione di carte destinate all’imballaggio; esse sono
impiegate quando si voglia ottenere una carta liscia e perfettamente non
assorbente.
Il loro uso, pertanto, è limitato
quasi totalmente alla fabbricazione di carta da scrivere.
Questa categoria comprende le sostanze
coloranti. Esse sono aggiunte per conferire alla carta determinati colori di
diverse tonalità. Allo scopo si impiegano terre coloranti, colori minerali e
coloranti all’anilina. L’uso di queste sostanze nel settore dell’imballaggio
è limitato alle carte destinate alle confezioni più fini, in quanto,
ovviamente, la loro aggiunta all’impasto comporta un aumento nel costo della
carta.
Le materie prime, quindi, vengono
messe assieme in un particolare impasto che si realizza, con l’aggiunta di
una determinata dose di acqua in speciali vasche ovali, dette olandesi, dove
un cilindro rotante, munito di lame, procede alla mescolazione dell’impasto e
alla sua raffinazione. Con il secondo sistema, anch’esso in uso, si procede
invece alla raffinazione separata dei singoli componenti che vengono
mescolati in una vasca con agitatore situata subito prima della macchina da
carta.
Questa consiste in tre parti distinte.
Nella prima l’impasto viene portato su un nastro a mezzo di opportuni
dispositivi che lo distribuiscono nel modo più uniforme possibile.
Successivamente, l’impasto viene pressato facendolo passare attraverso
particolari cilindri. Grazie a tale operazione viene eliminata una certa dose
di acqua che, chiamata acqua di recupero, viene convogliata in canali e viene
immessa nuovamente nel ciclo di lavorazione. La seconda parte della macchina
è costituita da una serie di cilindri riscaldati attraverso i quali passa
l’impasto, che, in tal modo, viene quasi completamente disidratato. Al
termine della lavorazione, infatti, la carta deve essere portata al 95% di
secco.
Ovviamente, quanto più lunga è questa
seconda sezione – e cioè quanto più elevato è il numero dei cilindri
essiccatori impiegati -, tanto più veloce è la disidratazione, e quindi la
fabbricazione della carta. Infine, la terza parte della macchina è costituita
da una bobinatrice che, accogliendo il foglio ancora leggermente caldo in
uscita dalla seconda sezione della macchina, lo avvolge in bobine di
determinate dimensioni, le quali vengono contemporaneamente rifilate dalle
due parti mediante appositi coltelli.
In alcuni casi è preferibile
suddividere la carta in fogli, anziché in rotoli. Oltre ai coltelli
longitudinali di rifilatura, si impiega allora anche una taglierina
trasversale che, a cadenza regolata normalmente a mezzo di un eccentrico con
la velocità di uscita del nastro di carta, taglia la carta stessa in fogli
delle dimensioni volute.
Con queste materie prime e con il
metodo di fabbricazione sopra descritto, si procede dunque alla realizzazione
della carta, sia essa destinata ad avvolgimenti o imballaggi singoli, o
destinata alla formazione del cartone ondulato; in questo caso, per
l’accoppiamento delle copertine e della parte ondulata interna vengono usate
colle all’amido o al silicato, di cui tratteremo in seguito.
Passiamo pertanto ad
esaminare le materie prime destinate alla fabbricazione del cartoncino,
segnalando che i cartoncini sono prodotti analoghi alla carta ma di peso
superiore, variabile tra i 50 e 400 g/m2, e di spessore pure superiore, che va
da 0,3 mm. in su.
La fabbricazione del cartoncino può
avvenire ad uno strato e in questo caso prende il nome di cartoncino naturale
– o a più strati.
L’utilizzo maggiore del cartoncino si
ha nella realizzazione di astucci pieghevoli; esso pertanto deve essere di
adatta rigidità e robustezza, di colore bianco e di superficie liscia per
poterlo stampare con le normali macchine offset.
Per la fabbricazione del cartoncino,
la materia prima fibrosa principale è la cartaccia. Ovviamente, più la
cartaccia impiegata è di buona qualità (carta Kraft, vecchie scatole di
cartone ondulato), più il cartoncino risulterà migliore. A tal scopo si
adoperano a volte pasta legno imbianchita, cellulosa Kraft e al bisolfito e
pasta semichimica. E poiché, di regola, il cartoncino è composto da 3 a 5
strati, si cercherà di unire gli strati in modo tale che all’esterno vi sia
lo strato di migliore qualità, seguito dallo strato interno e poi dagli
strati intermedi. Nel corso della fabbricazione vengono poi impiegate anche
sostanze coloranti (colori all’anilina), sostanze collanti (soda caustica,
allume, ecc,), sostanze di carica (pigmento di titanio, per rendere il
cartoncino bianco, e amido, per dare un aspetto fine alla sua superficie).
Molte volte il cartoncino viene
patinato sul lato esterno; per tale operazione si usano caolino e caseina.
Il procedimento di fabbricazione del
cartoncino non differisce molto da quello della carta; la macchina comprende
di regola una sezione con presse umide, una sezione per essiccare l’impasto,
un cilindro particolare per lucidare la parte esterna del cartoncino e
normali taglierine per la rifinitura e il taglio del cartoncino, all’uscita
della macchina.
Esaminiamo ora le materie
prime e i procedimenti impiegati per la fabbricazione del cartone. E’
necessario però, a questo punto, premettere una fondamentale distinzione fra
cartone solido (o rigido, o compatto) e cartone ondulato.
Procederemo quindi ad esaminare
separatamente i due tipi di cartone, segnalando che per gli imballaggi in
Italia viene utilizzato nella maggior parte dei casi il cartone ondulato.
Il cartone solido è costituito da un
foglio di materie fibrose vegetali pressate ed essiccate. Lo spessore è
superiore ai 2 millimetri e la grammatura
varia da 400 a 1200 g/m2. Le materie prime per la fabbricazione del
cartone sono diverse; gli stracci sono i più usati e, prima del loro impiego,
vengono fatti bollire con calce viva, per distruggere le eventuali fibre di
lana e per eliminare il colore degli stracci stessi. Viene usata anche la
pasta legno sia da sola che insieme alle altre materie. Le cartacce vengono
impiegate nella fabbricazione dei cartoni grigi. Il ciclo di lavorazione si
svolge nella maniera vista sopra per le carte e i cartoncini, dopo aver
proceduto alla collatura dell’impasto, all’aggiunta di sostanze di carica
(argilla e caolino) e alla colorazione con terre colorate o con colori
all’anilina. Evidentemente le macchine per la fabbricazione del cartone
solido differiscono in alcuni particolari (cilindro di pressione differenti e
in numero diverso, ecc,) ma, come abbiamo già fatto rilevare, la tecnica di
svolgimento dell’operazione è praticamente identica a quella seguita per la
carta e il cartoncino.
Per cartone ondulato si intende un
prodotto cartotecnico costituito, nella sua forma più semplice, da due strati
di carta liscia, detti copertine, fra cui è posto uno strato di carta
ondulata. Dalla sua prima realizzazione, avvenuta ad opera dell’americano
A.L. Jones nel 1871, il cartone ondulato ha avuto uno sviluppo progressivo e
quasi travolgente. La sua costituzione lo rende infatti particolarmente
indicato per l’impiego nel campo dell’imballaggio e la sua resistenza e
versatilità aprono per esso sempre nuovi settori di applicazione.
I cartoni ondulati si differenziano
tra loro sia per la diversa composizione e resistenza delle carte componenti
(di ciò tratteremo più avanti) sia per il diverso spessore del cartone
stesso, dato il numero degli strati e l’altezza dell’onda della carta
ondulata interna.
Abbiamo, quindi, per il cartone
ondulato, tre diversi tipi di onda: A, B e AB. L’onda A ha un’altezza di 5
millimetri, l’onda B di 3 millimetri e l’onda AB di 7,5-8 millimetri. Da
qualche tempo è stata realizzata all’estero anche l’onda E (o micro-onda).
L’onda E ha un’altezza di 1,5-1,8 millimetri e si presta molto bene ad essere
impiegata nella realizzazione di scatole ed astucci di medie e piccole
dimensioni.
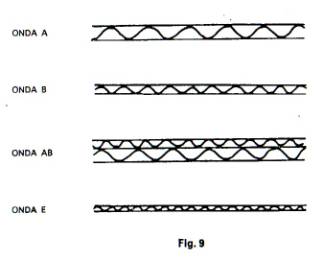
A seconda
della resistenza che si vuol dare al cartone, vengono adoperate copertine di
carta Kraft extra, Kraft, Duplex e Camoscio, le cui rispettive sigle, usate
per contraddistinguere i diversi tipi di cartone, sono le seguenti: Ke, K, D
e C. La carta migliore, più resistente e di più bell’aspetto, avente anche
maggior grado di stampabilità, è la carta K; seguono le carte Ke, D e, per
ultima, la carta C.
Per la parte ondulata esterna si usa
carta paglia (P), carta semichimica (S) e, ultimamente, carta rigenerata (R).
Per l’incollaggio delle copertine alla
parte ondulata si adoperano colle all’amido (a), al silicato di sodio (s), o
miste amido-silicato (m).
L’amido è una colla vegetale, di peso
inferiore al silicato (circa 20 grammi al metro quadrato di cartone),
solubile in acqua.
Ha un costo superiore al silicato, ma
deve essere adoperato in ogni caso quando si lavora su macchine per la
fabbricazione di cartone ondulato veloci (150-200 metri al minuto).
Il silicato, come già
detto, ha un costo inferiore all’amido e da maggior resistenza alla cassa, ma
ha un peso maggiore (80-100 grammi al metro quadrato di cartone); in presenza
di umidità segna le ondulazioni e, inoltre, vetrifica facilmente, costituendo
nella cassa di cartone ondulato una specie di armatura che dà rigidità e
maggior resistenza allo schiacciamento, ma presente l’inconveniente che le
falde di chiusura della cassa, dopo alcune piegature, si rompono, in quanto i
cristalli del silicato fungono da coltelli.
La fabbricazione del cartone ondulato
avviene su macchine speciali, da cui il cartone esce in larghezza variabile
da 160 cm. a 210 cm., a seconda del tipo di macchina, in modo da poter
eseguire l’ordinazione di casse la somma delle dimensioni delle quali
differisca il meno possibile dalla larghezza di macchina; in tal modo si
ottengono sfridi di lavorazione minimi.
Le macchine per la fabbricazione del
cartone ondulato operano da due bobine di carta da copertine e da una bobina
di carta da ondulazione che, opportunamente riscaldate, vengono unite assieme
mediante incollaggio. E’ opportuno ricordare che la parte ondulata – che
nella bobina si presenta liscia – viene ondulata a caldo mediante speciali
cilindri ( a circa 160° C., per vapore surriscaldato all’interno di essi) che
hanno in superficie le stesse ondulazioni da dare alla carta; un tempo si
formavano ondulazioni più dolci, ora invece i cilindri sono costruiti in modo
da realizzare ondulazioni ad angolo più acuto, che offrono maggior
resistenza. E’ ovvio che ad ogni tipo di ondulazione corrispondono cilindri
diversi.
Dopo l’incollaggio il cartone viene
moderatamente essiccato; all’uscita della macchina esso è ancora ben caldo e
pertanto, dopo averlo rifilato, grazie ad un dispositivo a coltelli situato
alla fine della macchina, e tagliato nella misura adatta per la costruzione
delle casse, grazie ad una normale taglierina, il cartone ondulato, suddiviso
in fogli, viene lasciato condizionare in ambiente adatto per alcuni giorni.
Durante il condizionamento il cartone aumenta la sua resistenza allo
schiacciamento dell’onda di circa il 50%.
Per maggior chiarezza, diamo qui di
seguito (fig. 10) un semplice schema illustrante il procedimento di
fabbricazione di un cartone ondulato doppio (onda AB).
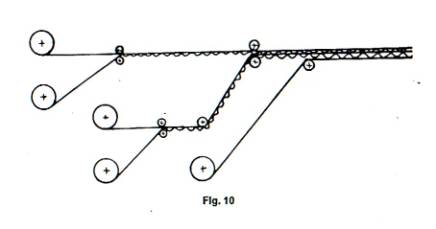
Come si nota dalla pur
schematica figura, nella fabbricazione del cartone ondulato doppio-doppio si
procede prima all’unione di una copertina con la parte ondulata, poi di
un’altra copertina (quella centrale del cartone) con una seconda parte
ondulata e quindi si unisce al tutto la terza copertina. E’ ovvio che
l’incollaggio avviene soltanto mediante speciali dispositivi sulla parte
delle ondulazioni destinata a venire a contatto con le copertine.
Il cellofan è il più
vecchio film d’imballaggio ed uno dei più largamente usati. Il suo vasto
impiego è dovuto al suo basso costo, alla sua trasparenza, alla facilità di
trasformarlo in imballaggio, alla possibilità di essere accoppiato con
materie plastiche per effettuare la termosaldatura e per ridurre
l’assorbimento di umidità.
La materia prima per la fabbricazione
del cellofan è la cellulosa di legno imbianchita che, opportunamente trattata
con soda caustica, si trasforma in sostanza colloidale. Questa sostanza, dopo
vari trattamenti, viene ridotta in un film di cellulosa trasparente, che
costituisce appunto il cellofan. Il cellofan è quindi derivato da fibre
vegetali e non sintetiche, è un film di cellulosa e non un film di materia
plastica.
Per la migliore realizzazione
dell’imballaggio, soprattutto se questo è formato su attrezzature ad alta
velocità, è essenziale il controllo del contenuto di umidità del cellofan;
tale percentuale ha influenza sulla flessibilità, al cellofan vengono
aggiunti spesso plastificanti. Va ricordato che un cambiamento nel contenuto
di umidità provoca un cambiamento nelle dimensioni del film. Tale cambiamento
è più rilevante nella direzione trasversale che nella direzione macchina.
Come nella carta, invece, la resistenza alla trazione è superiore nella
direzione machina che nella direzione trasversale.
Il cellofan viene facilmente saldato
con adesivi e la sua struttura ne fa un materiale particolarmente resistente
ai grassi, alla polvere e ai germi. Se il film è asciutto, il cellofan è
discretamente resistente al passaggio dei gas, se il film contiene umidità,
aumenta la percentuale di gas assorbito.
Descritti così brevemente i metodi di
fabbricazione e le materie prime per la realizzazione della carta, del
cartone e del cellofan, passiamo ad esaminare i singoli imballaggi che
vengono prodotti con i materiali sopra descritti.
IMBALLAGGI DI CARTA E
CARTONCINO
Carta e cartoncino sono
tuttora tra i materiali di imballaggio più usati: la carta grazie alla sua
versatilità, il cartoncino per la resistenza che offre accompagnata tuttavia
da una discreta flessibilità e dalla possibilità di venire stampato a più
colori in maniera perfetta, grazie alla moderna macchina offset. Carta da
avvolgere, buste, sacchetti, shoppings, sacchi a medio e grande contenuto,
scatole e astucci rigidi e pieghevoli, sono i più usati imballaggi realizzati
in carta e cartoncino.
Di essi, qui di seguito, descriviamo
le principali caratteristiche e finalità.
CARTA DA AVVOLGERE
Per la carta da avvolgere
s’intende un semplice foglio di carta con cui viene avvolto normalmente il
prodotto destinato alla vendita. E’ ancora possibile riscontrare,
specialmente nei piccoli centri di provincia e anche nei negozi di periferia,
l’uso in grande quantità di tale tipo di carta per avvolgere una vasta gamma
di prodotti, soprattutto alimentari.
Citeremo fra essi la carne, gli
affettati, a volte il pane, lo zucchero, la farina, la frutta. L’uso di
questo sistema di confezionamento va tuttavia man mano diminuendo, in quanto
viene soppiantato dall’impiego di sacchetti o buste a seconda dei casi che
permettono la chiusura dell’imboccatura e quindi danno la possibilità di
vendere i prodotti a peso controllato. Nel caso della frutta, che ha bisogno
di “respirare” e che può inumidire la carta, essa viene posta soltanto
all’atto della vendita in sacchetti a bocca aperta. E’ opportuno comunque
segnalare che la grammatura della carta – compresa la carta oleata per
prodotti oleosi o grassi -, come pure la sua composizione, possono variare
notevolmente a seconda delle richieste dell’utilizzatore e, naturalmente,
della varietà dei tipi prodotti dalle cartiere che, per esigenze di costi, ne
producono un limitato numero di diverse qualità.
Esistono ad esempio carte paraffinate,
carte resistenti ai grassi e all’umidità, oltre ad una vasta serie di carte
accoppiate con foglio sottile di alluminio o films plastici, di cui
tratteremo nel capitolo riguardante le materie plastiche. Esistono anche
carte speciali con cui vengono avvolte parti di macchine e oggetti delicati
per la spedizione.
Ovviamente il prodotto così avvolto
deve essere successivamente imballato in modo adeguato; di queste particolari
carte tratteremo comunque nel capitolo riguardante gli accessori.
BUSTE,
SACCHETTI, SHOPPINGS
Normalmente, per buste di
carta si intendono le comuni buste per corrispondenza, che hanno un
vastissimo impiego nel settore del commercio e di cui illustriamo i tre tipi
più usati (fig. II).
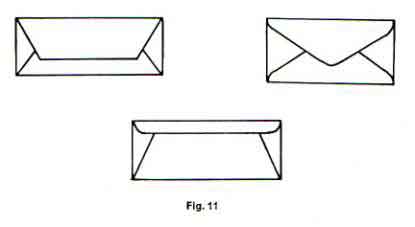
Vengono
usati tuttavia altri tipi di buste, più grandi e di differente forma,
foderate o meno, per la spedizione di libri e riviste.
Ne illustriamo i tipi più
correnti (fig. 12)
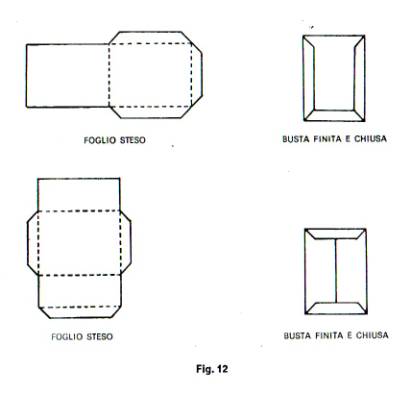
Quasi
tutte le qualità di carta sono adatte alla fabbricazione di buste, la scelta
dipende dall’uso che di tali buste si vuol fare; la chiusura avviene di
regola con adesivo, la stampa può essere effettuata su entrambi i lati della
busta con i più diversi sistemi.
La sostanziale differenza tra buste e
sacchetti sta nel sistema di chiusura. Infatti nelle buste la chiusura
avviene grazie ad una piccola falda che va sovrapposta e incollata ad un lato
della busta stessa.
Nei sacchetti la chiusura avviene a
mezzo graffette metalliche a mezzo spago, o più semplicemente con una doppia
piegatura manuale. Una gran parte dei sacchetti viene fabbricata con un
soffietto laterale, del tipo qui illustrato (fig. 13).
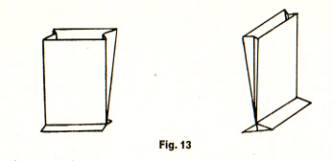
Anche i sacchetti
possono venire fabbricati con i più diversi tipi di carta: carta al solfito e
carta Kraft soprattutto.
A volte i sacchetti vengono realizzati
a parete doppia (in pratica con due strati di carta) quando si vuole ottenere
una resistenza elevata o per particolari utilizzazioni.
Per shoppings si intendono particolari
tipi di sacchetti, di forma parallelepipeda, più bassi e larghi dei sacchetti
normali e dotati di maniglie, generalmente di carta resistente o spago o
fettuccia.
Sono realizzati in una più larga
varietà di dimensioni e tipi di carta, e il loro uso è indicato per il
trasporto a casa dei prodotti acquistati nei grandi magazzini. Ecco, qui
illustrato, un tipo di shopping (fig. 14).
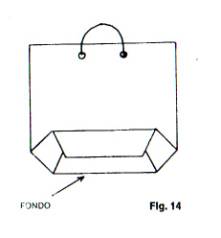
SACCHI A
MEDIO E GRANDE CONTENUTO
I sacchi di carta a medio
e grande contenuto sono imballaggi costituiti da più strati di carta e
destinati a contenere materiali polverulenti o granulari per la spedizione.
Il loro uso è stato recentemente limitato dall’avvento dei sacchi in
plastica, mentre i sacchi di carta avevano, a suo tempo, ridotto notevolmente l’impiego dei sacchi
di juta.
Il sacco di carta, comunque, è tuttora
largamente usato per il trasporto dei prodotti in polvere meno pregiati
(calce, gesso, cemento, in parte fertilizzanti, ecc.). Il peso lordo di
questi imballaggi varia da 10 a 50 Kg.
Per la loro costruzione si impiegano
generalmente fogli di carta Kraft (in numero da 2 a 5) di grammatura
variabile dai 60 agli 80 g/m2, anche bitumati, avvolti a forma di tubo,
mediante incollaggio o cucitura laterale (per i sacchi che devono presentare
più resistenza) e chiusi ad una estremità (fondo) mediante incollaggio.
L’altra estremità (imboccatura) può essere a bocca aperta o a valvola. Il
sacco è a bocca aperta quando l’imboccatura è completamente aperta e la
chiusura avviene, a prodotto introdotto, a mezzo spago, a mezzo punti
metallici o mediante cucitura (fig. 15).
I sacchi a valvola sono sacchi di
carta la cui imboccatura non è aperta, bensì chiusa con un metodo simile a
quello usato per la chiusura del fondo.
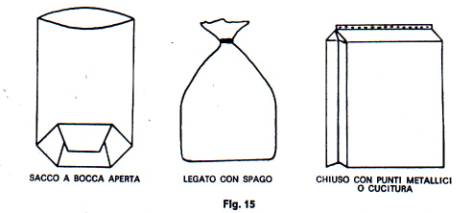
Viene
lasciata però, da un lato, una piccola apertura, munita di un manicotto pure
in carta, attraverso il quale viene introdotto il materiale nel sacco. Quando
il sacco è pieno, è lo stesso contenuto che opera una pressione sul
manicotto, chiudendolo ed impedendo così l’uscita del prodotto (fig. 16).
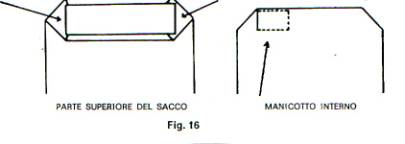
Sia
per i sacchi a bocca aperta che a valvola, vengono usate per il riempimento
particolari bilance automatiche di elevata precisione, munite di
trasportatori per l’evacuazione del sacco, che viene trasportato a magazzino
e che viene sostituito manualmente dall’addetto alla macchina, con
l’applicazione di un altro sacco sul dispositivo erogatore del prodotto.
SCATOLE E ASTUCCI RIGIDI
PIEGHEVOLI
Le scatole di cartoncino
rigide sono scatole che vengono fornite dal fabbricante all’utilizzatore già
montate e con il coperchio a parte. Vengono usate, nella maggioranza dei
casi, con all’interno inserto o alveari, in modo da suddividere il prodotto
contenuto. Il montaggio della scatola viene effettuato con punti metallici,
con nastro gommati o con rivestimenti di carta stampata, nei casi in cui si
voglia un imballaggio di una certa eleganza. In altri casi il rivestimento di
carta, viene applicato alla parete di fondo della scatola e quindi ripiegato
per la chiusura della scatola stessa. Altre volte il coperchio è costituito
da un manicotto che avvolge completamente la scatola. L’apertura e la
chiusura, in questo caso, avvengono facendo scorrere a pressione la scatola
entro il manicotto costituito dal coperchio.
Scatole e astucci pieghevoli hanno un
metodo di costruzione completamente diverso. Il cartoncino da usare per la
realizzazione dell’astuccio viene dapprima stampato a più colori –
generalmente su macchine offset -, riproducendo in tal modo più volte (tante
quante è possibile in un foglio di cartoncino di centimetri 70 x 100) il
disegno che avrà l’astuccio.
Il cartoncino viene poi fatto passare
su speciali macchine, dove viene fustellato e cordonato. La fustellatura è
un’operazione singola mediante la quale viene tagliato il contorno
dell’astuccio in piano e vengono, nello stesso tempo, effettuati tutti i
tagli necessari al montaggio della scatola. La cordonatura è un’operazione
mediante la quale vengono praticate sul cartoncino tutte le linee di
piegatura per l’erezione dell’astuccio.
Nel disegno qui riprodotto (fig. 17)
abbiamo cercato di illustrare nel modo più semplice
possibile la tecnica di costruzione di
un astuccio pieghevole. Il riquadro ABCD costituisce il foglio di cartoncino
all’interno del quale, per comodità, abbiamo disegnato un solo astuccio,
mentre in realtà il numero di astucci che si ricava da un foglio è maggiore e
varia ovviamente a seconda delle dimensioni dell’astuccio stesso.
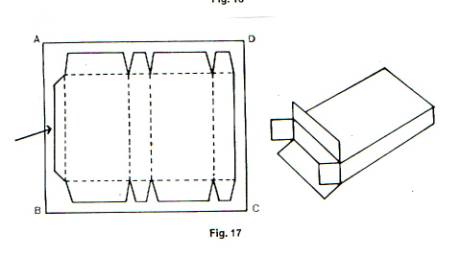
L’astuccio è
disegnato con linee continue e linee tratteggiate. Le linee continue indicano
l’operazione di fustellatura, quelle tratteggiate l’operazione di
cordonatura. A destra l’astuccio montato. L’astuccio però non viene fornito
all’utilizzatore già montato, ma appiattito, con la sola incollatura della
falda laterale longitudinale (indicata nella figura con la freccia) all’altra
estremità dell’astuccio, in modo da formare una specie di tubo, appiattibile
grazie alle cordonature. Gli astucci così formati, una volta giunti all’utilizzatore,
vengono eretti, incollati dalla parte del fondo, riempiti, incollati anche
dalla parte da cui sono stati riempiti e sistemati nelle casse di spedizione,
il tutto con l’ausilio di un’unica macchina che svolge da sola tutte le
operazioni.
E’ ovvio che le forme
degli astucci e delle scatole sono molteplici: per ognuna di esse vi sono particolari macchine atte a
svolgere le sopra citate operazioni.
ALTRI TIPI DI IMBALLAGGI
Vogliamo qui ricordare le
confezioni in pasta di cellulosa pressata, la cui fabbricazione avviene
mediante speciali stampi di pressione a caldo. Con tale procedimento vengono
prodotti vassoi di varie forme e colori per la presentazione della frutta e
della carne nei supermercati (il tutto normalmente avvolto in film di materia
plastica termoretraibile) e confezioni particolari per la vendita delle uova.
Ricordiamo anche i fusti
cilindrici di fibra, realizzati con un avvolgimento continuo di carta fino
alla formazione del corpo cilindrico, cui successivamente vengono applicati,
generalmente mediante cerchioni di metallo, il fondo e il coperchio. Di
regola all’interno il fusto viene rivestito con uno strato di polietilene
impermeabile. Il fusto così realizzato consente l’imballaggio per la
spedizione dei più svariati prodotti, particolarmente granulari o in polvere,
anche igroscopici. L’avvolgimento continuo della carta può essere a spirale,
quando la carta viene avvolta elicoidalmente attorno all’anima interna
cilindrica, oppure perpendicolarmente sovrapposto, quando nell’avvolgimento gli
strati della carta vengono sovrapposti esattamente l’uno sull’altro.
IMBALLAGGI IN CARTONE
Importanza fondamentale
nel settore imballaggio hanno i prodotti cartotecnici derivati dalla
lavorazione del cartone solido e, soprattutto, ondulato. Non è il caso di
elencare particolareggiatamente gli innumerevoli campi di impiego delle casse
di cartone; è sufficiente ricordare che esse vengono impiegate nella maggior
parte delle spedizioni dei prodotti all’interno del Paese e su vasta scala
anche nelle spedizioni all’estero. E’ opportuno quindi trattare
specificatamente delle casse in cartone solido e di quelle in cartone
ondulato onde rendersi conto, con la miglior chiarezza possibile, della
tecnica di costruzione di questi tipi di imballaggio.
CASSE IN CARTONE SOLIDO
Le casse in cartone
solido, il cui uso all’estero è abbastanza elevato – specialmente negli Stati
Uniti -, non sono molto impiegate in Italia nella spedizione dei prodotti.
Ciò dipende in gran parte dal maggior costo che esse presentano rispetto a quelle
in cartone ondulato e anche dal fatto che, di conseguenza, fabbricanti e
trasformatori di cartone si sono attrezzati soltanto con macchine adatte alla
produzione e alla lavorazione dell’ondulato.
La materia base è il cartone solido,
della cui fabbricazione abbiamo trattato in precedenza; il sistema di
lavorazione è più o meno analogo a quello delle scatole in cartoncino rigide.
Per la formazione del corpo e del coperchio si procede fissando i lati della
cassa con colla o con graffe metalliche, come mostra il disegno (fig. 18).
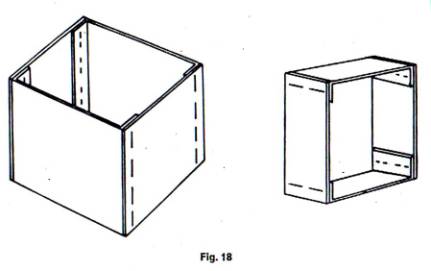
Un
altro tipo di casse di largo impiego è il seguente, mostrato nel disegno
prima in piano e poi montato (fig. 19). Ricordiamo che le linee tratteggiate
indicano le cordonature e le linee continue le fustellature.
A volte le casse in cartone solido,
specialmente per spedizione oltremare, vengono trattate con cere microcristalline,
al fine di renderle impermeabili all’umidità ed alla salsedine.
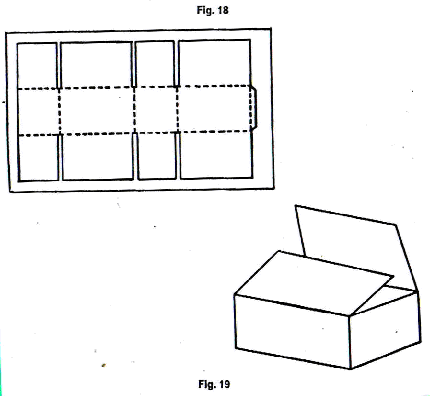
CASSE IN
CARTONE ONDULATO
Abbiamo già visto come avviene
la fabbricazione del cartone ondulato, sia esso ad onda alta, ad onda bassa o
doppio-doppio.
Non ci resta quindi che esaminare la
tecnica di fabbricazione delle casse. E’ necessaria qui subito una
suddivisione tra casse modello “americano” e casse modello “a telescopio”.
Queste ultime sono costituite da due parti, il fondo e il coperchio,
realizzate in modo tale che il coperchio si innesti perfettamente sul fondo,
fino alla base dello stesso. Le casse modello americano ,che sono le più
comuni, vengono fabbricate partendo da un foglio di cartone steso, che viene
opportunamente fustellato e cordonato (fig. 20).
Le linee tratteggiate indicano la
cordonatura del cartone, la linea continua indica la fustellatura.
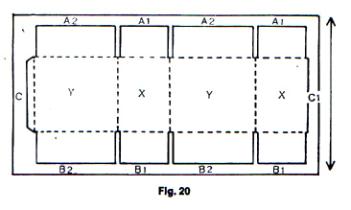
E’ opportuno segnalare
che normalmente la stessa macchina
che esegue la cordonatura e la fustellatura, esegue anche l’operazione di
stampa. Una macchina di questo tipo è chiamata “printer-slotter” e può
stampare sul cartone ondulato fino a quattro colori. La stampa diminuisce
leggermente la resistenza del cartone e, ovviamente, più colori vengono
impiegati, più questo indebolimento è rilevante. Segnaliamo anche che di
regola il cartone ha colore avana. E’ conveniente, dal punto di vista
economico, richiedere un altro colore per la copertina esterna soltanto se si
tratta di una grossa ordinazione.
Le pareti laterali di minor
dimensioni, contrassegnate con lettera x, si chiamano testate, quelle più
grandi, contrassegnate dalla lettera Y, si chiamano fiancate. Le parti
fustellate, contrassegnate con le lettere A1, A2 e B1, B2 si chiamano falde e
sono realizzate allo scopo di costituire rispettivamente il fondo e la
chiusura superiore della cassa di cartone. La piccola falda laterale C, nella
costruzione, va incollata o cucita con punti metallici alla parete opposta
C1. Come resistenza, l’incollaggio è leggermente superiore alla cucitura: è
pertanto preferito quando i punti metallici possono rovinare il contenuto;
non è però da usarsi se la cassa deve restare per lungo tempo in magazzini
umidi o deve essere spedita in località umide. La cucitura avviene con
macchine automatiche o semiautomatiche. E’ buona norma esigere che i punti
metallici abbiano una larghezza minima di 3 millimetri (salvo che nelle casse
di minime dimensioni, dove può venire usato anche filo metallico), siano
posti al massimo ad una distanza di 5 centimetri l’uno dall’altro e con una
inclinazione di 45 gradi rispetto alla direzione dell’ondulazione; inoltre
all’inizio e alla fine della cucitura devono essere posti due punti molto
ravvicinati fra loro. In qualche caso la piccola falda laterale non viene
realizzata; pertanto la chiusura laterale avviene a mezzo nastratura. Si deve
usare un nastro di opportuna resistenza, preferibilmente nastro sisal o
catramato, di grammatura non inferiore ai 70-90 g/m2, a seconda del tipo di
nastri e delle dimensioni della cassa.
La cassa con nastratura laterale è
però naturalmente più debole di quelle con cucitura o incollaggio.Nel disegno
appare anche una freccia verticale che indica il senso dell’ondulazione, che
è parallelo alla direzione trasversale del cartone quando esce dalla macchina
che lo fabbrica e perpendicolare alla direzione macchina. Poiché, per offrire
resistenza la cassa deve essere realizzata con la direzione dell’onda
verticale, è bene tener presente, nel calcolare l’altezza della scatola,
anche la larghezza massima del foglio di cartone ondulato (vedi la parte
dedicata alla fabbricazione del cartone).
Pertanto la cassa viene spedita dal
fabbricante all’utilizzatore in piano e verrà poi da questi montata, come
mostra il disegno (fig. 21).
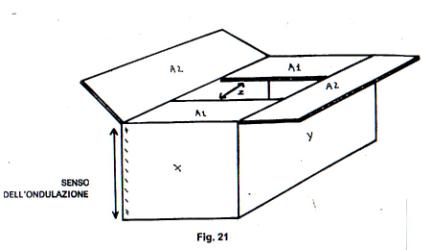
Sia per il
fondo che per la chiusura superiore della cassa, si piegano prima le falde
più corte A1 e quindi quelle più lunghe A2, che chiudono completamente la
cassa. Le falde A1 combaciano esattamente soltanto nel caso che la cassa
abbia le pareti X e Y di uguale lunghezza; anche negli altri casi ciò è
possibile ma comporta un notevole aumento nel costo della scatola, poiché gli
sfridi di lavorazione vengono aumentati in misura considerevole. Pertanto di
regola viene posto, tra le falde A1 (e cioè nello spazio Z della figura), un
ritaglio di cartone ondulato, anche di qualità inferiore, chiamato
interfalda. Le chiusure del fondo e della parte superiore avvengono con i
consueti metodi di cucitura, nastratura e incollaggio. Va ricordato che
l’incollaggio rende più difficile l’apertura della cassa e che la nastratura
deve essere effettuata in modo che il nastro gommato venga ripiegato lungo le
testate della cassa per un tratto pari a circa 1/3 delle stesse.
La cassa di cartone ondulato è così
completata. Resta da dire che all’interno in molti casi vengono inseriti dei
divisori in cartone per suddividere il contenuto. Si chiamano tramezze
trasversali quei fogli di cartone ondulato che suddividono la cassa nel senso
orizzontale, intercalari quei fogli che la suddividono nel senso verticale.
Vi possono essere inoltre il sottofondo – e cioè un foglio di cartone posto a
rinforzo sull’intera superficie del fondo della cassa - , e la faccia interna
che viene posta in modo da rivestire completamente all’interno le quattro
pareti della cassa. Infine gli alveari, costituiti da fogli di cartone
intersecantisi perpendicolarmente in modo da formare degli alveoli, dove
trovano posto generalmente bottiglie di vetro o altri prodotti dell’industria
del vetro e della ceramica.
Non esiste una unificazione italiana
dei tipi di cartone ondulato, ma ne esiste soltanto la classificazione, per
la quale consigliamo agli interessati di consultare le tabelle pubblicate dal
G.I.F.C. (gruppo italiano fabbricanti cartone ondulato); per l’unificazione dei tipi di casse,
consigliamo agli interessati le visioni delle tabelle F.E.F.C.O. (Fédération
Européenne des Fabricants de Carton Ondulé). Dette tabelle possono essere richieste
alle rispettive associazioni.
Vogliamo infine accennare agli
speciali imballaggi in cartone ondulato, chiamati fustellati. Sono
generalmente costituiti da un unico foglio di cartone ondulato di buona
qualità, che viene opportunamente fustellato e cordonato e che viene poi
montato manualmente per formare, a mezzo appositi incastri, imballaggio,
senza impiego di punti metallici, collanti e nastri adesivi. Si possono così
formare, con una discreta dose di inventiva e di genialità, innumerevoli tipi
di imballaggi, soprattutto per la presentazione di bottiglie di vino e
liquori, barattoli, ecc.
Di regola viene impiegato cartone
ondulato ad onda bassa di elevata resistenza, in modo da permettere una
agevole e sicura manipolazione per il montaggio delle confezioni, con il
minimo pericolo di rotture dovute alle piegature ed agli incastri del
cartone.
IMBALLAGGI DI CELLOFAN
Soprattutto per la vasta
gamma dei prodotti alimentari, numerosissime sono le possibilità che il
cellofan può fornire. La sua trasformazione in confezioni viene partendo da
bobine. Esse devono essere tenute in magazzino sollevate da terra, ad una
temperatura di 18-20 gradi e al 55-60% di Umidità Relativa. Ciò perché il
cellofan, come già visto, assorbe facilmente umidità. Normalmente il cellofan
viene rivestito con materiali termoplastici (copolimeri di vinile, politene)
per unire alla resistenza meccanica del cellofan impermeabilità al vapor
acqueo e la possibilità di termosaldatura delle materie plastiche. Grande
utilizzo di questi accoppiati si ha nelle macchine “form and fill” che
lavorano in verticale o in orizzontale partendo dalla bobina di accoppiato.
Nelle macchine orizzontali si
confezionano prodotti solidi e di una certa dimensione (prodotti da forno ad
esempio), attorno ai quali automaticamente la macchina avvolge l’accoppiato e
lo salda in senso longitudinale; un successivo dispositivo salda l’accoppiato
in senso trasversale dividendolo in
tante piccole confezioni, contenenti ciascuna una data quantità di prodotto.
Nelle macchine verticali si confezionano prodotti granulari o solidi di
piccole dimensioni (pop corn, caramelle) e in questo caso il prodotto cade,
nella quantità voluta, nell’avvolgimento di accoppiato realizzato con lo
stesso procedimento delle macchine orizzontali.
Tratteremo comunque ancora del
cellofan e degli accoppiati nel capitolo che riguarda le materie plastiche.
VETRO
I contenitori di vetro
possono essere usati per quasi tutti i prodotti solidi, liquidi e pastosi.
Particolarmente però essi vengono usati nelle confezioni di prodotti
alimentari, bevande e prodotti farmaceutici, cosmetici e di profumeria. Già
in precedenza abbiamo parlato delle origini del vetro, della sua storia
vecchia almeno di 3000 anni e di come esso abbia assunto nel corso dei secoli
una posizione di preminenza nel campo dell’imballaggio, posizione mantenuta
anche dopo l’avvento di nuovi materiali.
Il vetro è disponibile in una vasta
gamma di colori, ha particolari composizioni chimiche che vengono di volta in
volta leggermente variate a seconda delle necessità, ha una trasparenza
eccellente, una superficie liscia e presenta resistenza notevolissima agli
agenti chimici.
Inoltre è perfettamente igienico,
chimicamente inerte e impermeabile a gas, liquidi, umidità.Per contro, il
punto negativo del vetro è la sua fragilità, che lo rende particolarmente
delicato soprattutto nelle spedizioni.
Ma non vogliamo qui per il momento
dilungarci troppo sulle caratteristiche del materiale. Vogliamo invece
illustrare il procedimento di fabbricazione che rende le materie prime atte
alla trasformazione di imballaggi di vetro delle più diverse forme e
dimensioni.
Materie prime
La materia prima di base
è il componente principale del vetro la silice (Sio2), che da lo stato
cristallino, riscaldata ad oltre 1700° passa allo stato amorfo e può essere
modellata nelle forme più diverse.
Ovviamente, altre materie prime
entrano a far parte del vetro: così abbiamo i vetrificanti (silice e anidride
borica), e solventi (carbonato di sodio e di potassio) le sostanze stabilizzanti
(sesquiossido di alluminio, carbonato di calcio, carbonato di calcio e
magnesio), le sostanze affinanti (solfato di sodio e sesquiossido di
arsenico), e sostanze decoloranti (manganese). Abbiamo poi le sostanze
coloranti (sesquiossido di ferro, sesquiossido di cromo, ecc.).
Mentre la silice fonde ad oltre 1700°,
la miscela delle sopra elencate sostanze – opportunamente dosate a seconda
del tipo di vetro che si vuole ottenere - , posta in forni di materiale
refrattario, fonde a circa 1560°; può fondere anche a circa 1520° con un
rendimento però inferiore del 20%. La massa fusa viene successivamente
purificata mediante l’eliminazione delle scorie di lavorazione e quindi
portata in speciali stampi, dove prende la forma del contenitore. Esistono tre
procedimenti per la fabbricazione del contenitore: il procedimento ad
aspirazione, il procedimento a doppio soffiaggio e il procedimento di
pressatura e soffiaggio.
Nel procedimento di aspirazione
(suction process) la massa fusa viene aspirata da un ugello aspiratore entro
uno stampo, fino al completo riempimento dello stampo stesso. La parte
superiore dello stampo ha la forma del collo della bottiglia da formare; in
questa operazione vengono pertanto formati il collo e l’imboccatura della
bottiglia.
Successivamente la forma di vetro
viene trasferita in un secondo stampo, dove un getto d’aria, che entra
dall’imboccatura della bottiglia precedentemente formata, fa aderire il vetro
alle pareti dello stampo, dando così alla bottiglia la forma voluta e definitiva.
Nel procedimento a doppio soffiaggio
(Blow and blow process) una goccia di massa fusa viene fatta cadere in uno
stampo che, nella parte inferiore, ha la forma del collo della bottiglia da
modellare. Grazie a due ugelli che fanno entrare due successivi getti d’aria,
uno dall’alto e uno dal basso, vengono formati il collo e l’imboccatura della
bottiglia. Con una seconda operazione la forma di vetro – che si presenta
oblunga – viene fatta uscire dal primo stampo, capovolta in modo da portare
l’imboccatura della bottiglia verso l’alto e inserita in un secondo stampo
dove, a mezzo di un altro getto d’aria che penetra attraverso l’imboccatura, le si conferisce la forma definitiva.
Nel procedimento di pressatura e
soffiaggio (press and blow process) – impiegato nella fabbricazione di vasi e
vasetti di vetro -, una goccia di vetro fuso viene fatta cadere in uno stampo
a larga imboccatura, entro la quale penetra un pistone di forma speciale, che
comprime il vetro e forma in tal modo il collo e l’imboccatura del vaso.
Successivamente la forma di vetro viene portata nel secondo stampo dove,
sempre a mezzo di un getto di aria, essa prende la forma definitiva del vaso.
Quando
l’imballaggio esce dalla macchina formatrice, la sua superficie esterna è
rigida ed ha una temperatura di circa 300, la parte interna è ancora calda e
molle. Se il raffreddamento continuasse normalmente, la parte interna si
contrarrebbe più di quella esterna: sorgerebbero così tensioni interne che
potrebbero essere anche di una certa gravità. Per ovviare a tale
inconveniente si fanno passare gli imballaggi in un tunnel, dove vengono
riscaldati a 550°. In questo modo si rifonde leggermente la superficie
esterna degli imballaggi, che successivamente vengono lentamente raffreddati.
Durante il susseguirsi delle operazioni, importantissimo è il controllo delle
dimensioni e della capacità del prodotto. Una capacità, la più costante
possibile garantisce l’utilizzatore nella fase di riempimento
dell’imballaggio. Dimensioni costanti significano uniformità nell’aspetto
della confezione in vetro e, se si prende in considerazione lo spessore delle
pareti, all’uniformità dell’aspetto si aggiunge la sicurezza di un uniforme
standard di resistenza delle bottiglie stesse.
A questo proposito, è opportuno
segnalare che le parti di un contenitore di vetro che offrono meno
resistenza, sono gli spigoli. In linea teorica l’imballaggio più resistente
sarebbe a forma di sfera, in quanto ogni urto verrebbe assorbito dall’intera
superficie dell’oggetto. In pratica però – a parte l’esempio dei fiaschi per
vino, che si presentano quasi sferici – gli imballaggi di vetro si presentano
normalmente cilindrici, con gli spigoli arrotondati (fig. 22).
|